
Our Work
At Progressive Handling Inc, we take pride in crafting tailored solutions to meet our customers' unique needs. Here are just a few examples of how we've successfully assisted our clients: from optimizing workflow processes to implementing innovative handling systems, we are dedicated to delivering results that make a difference. Let us help you find the right solution for your challenges!
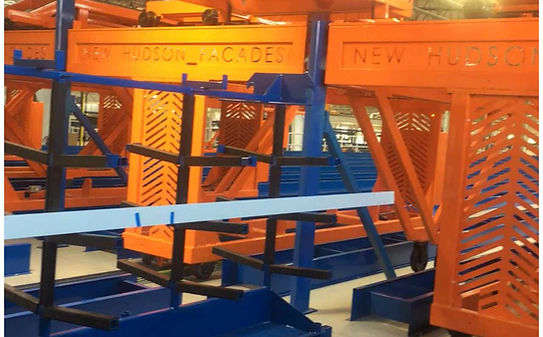
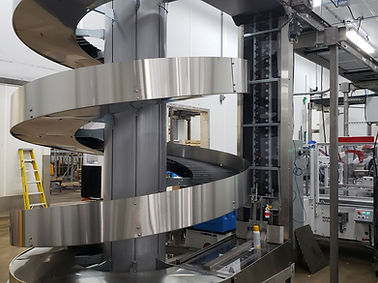
01
Upper Iowa Beef
UIB came to PHI looking to go from processing 200 head of cattle per week to 1200 head. PHI delivered a system that not only enabled the 1200 but is currently producing at over 2000 head weekly.
02
Viking Spas
Viking Spas needed to increase the number of stock carrying units without increasing the square footage requirements. PHI engineered and provided a system that allowed Viking to increase from 15 SKU to 60.
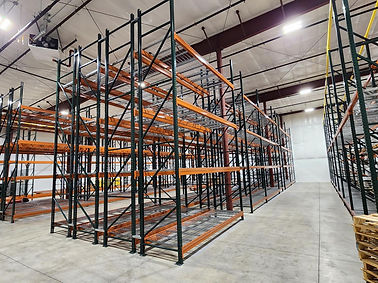
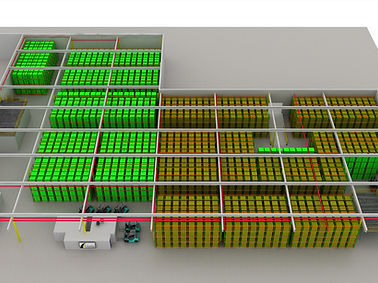
03
Columbian Logistics
Customer growth required CLN to get more cubes of storage into the same 4 walls. PHI was able to analyze their need and get them 25% more storage than other providers by utilizing a drive-in-rack system.
04
Nice Pak
PHI was asked to find a method of placing a sticker on the two sides of a stack of wet ones so individual cartons holding the stacks prior to cartoning could be eliminated. This was as a result of a failed robotic solution by an unknown vendor
The challenges were:
-
Stack ranged from two to six high
-
The stack had to be aligned within ¼”
-
The rate was 100 single high units from production
The first thing we did was build a mockup of our stacking device and then proceeded to develop the equipment around the stacker. To accomplish this, we divided the flow into two incoming streams of 50 per minute. The success of this system was duplicated three times.
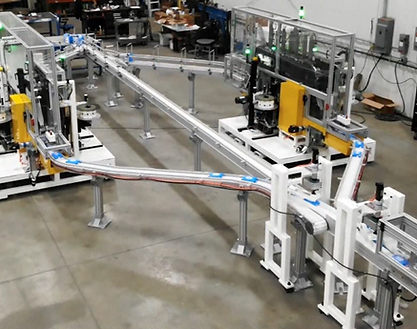
05

New Hudson Facades
PHI was asked to develop a storage and retrieval system for large racks of Façade components ready to be kitted or sent to assembly. The challenges were:
-
The size of the carts
-
The space available
-
The tracking system and method to deliver the racks to a large mezzanine.
-
Keeping inventory up to date and keeping the space full.
Our custom design solved all these considerations providing a functional custom storage and retrieval system.
06
Houston Foodbank
PHI was presented with a standard bud request for a floor conveyor system to make sorting food into deliverable cases of roughly 50# each. After reviewing the bid request, it became evident that floor conveyor was not the best solution. So, we designed both an overhead conveyor solution and a special carrier to accomplish the desired results. The result was a system that from day one more than doubled the output for food boxes ready for delivery.
